In the world of fabrication, precision is paramount. Every cut, every angle, every piece matters. Oxyfuel track torch cutting emerges as a game-changer, offering unparalleled accuracy and efficiency. In this comprehensive guide, we delve into the usage, affordability, significance, and mechanics of oxyfuel track torch cutting, uncovering why it's a must-have in any fabrication business arsenal.
Using an oxyfuel track cutting torch requires careful setup and operation to ensure safe and precise cutting. Below is a step-by-step guide on how to use the oxyfuel track cutting torch effectively:
Step 1: Preparation
- Ensure you have the necessary safety equipment, including gloves, goggles, and a welding helmet with a suitable shade.
- Select the appropriate track system for your cutting application and ensure it is securely set up on the workpiece.
- Check that the cutting torch, hoses, and gas supplies are in good condition and properly connected.
Step 2: Adjusting Gas Settings
- Set the appropriate gas pressures for oxygen and fuel gas (usually acetylene or propane) according to the manufacturer's recommendations.
- Adjust the oxygen and fuel gas valves on the torch handle to achieve the desired flame characteristics for cutting.
Step 3: Preheating
- Position the torch at the starting point of the cut on the workpiece.
- Open the fuel gas valve and ignite the gas using a suitable ignition device, such as a striker or a torch igniter.
- Gradually open the oxygen valve to introduce oxygen into the flame, preheating the workpiece until it reaches the required temperature for cutting.
Step 4: Cutting
- Once the workpiece is preheated, move the torch along the pre-marked cutting path at a steady pace, following the track system.
- Continue to adjust the oxygen and fuel gas valves to maintain the desired cutting speed and quality.
- Ensure that the torch remains perpendicular to the workpiece to achieve a straight and clean cut.
- As you progress along the cutting path, be mindful of any slag buildup that may occur behind the torch. Use a slag hammer or chipping tool to remove excess slag to maintain cutting quality.
Step 5: Post-Cutting
- After completing the cut, close the oxygen and fuel gas valves on the torch handle.
- Allow the workpiece to cool down before handling it to prevent burns or injuries.
- Inspect the cut for any defects or rough edges, and make any necessary adjustments or clean-up.
Step 6: Safety Precautions
- Always wear appropriate personal protective equipment (PPE) and ensure proper ventilation in the cutting area to prevent exposure to harmful fumes and gases.
- Keep a fire extinguisher nearby in case of emergencies.
- Never leave the torch unattended while it is lit, and always shut off the gas supply when not in use.
By following these steps and adhering to safety guidelines, you can effectively use an oxyfuel track cutting torch to achieve precise and efficient cuts in various fabrication applications.
Why Oxyfuel Track Torch Cutting?
1. Precision Redefined: Oxyfuel track torch cutting is renowned for its precision. It ensures clean, accurate cuts, even on the toughest of materials. Whether it's thick steel plates or intricate designs, this method delivers results with unparalleled accuracy.
2. Versatility: From small-scale projects to large industrial applications, oxyfuel track torch cutting adapts seamlessly. Its versatility makes it suitable for a wide range of fabrication tasks, including shipbuilding, construction, and manufacturing.
3. Cost-Effectiveness: Despite its advanced capabilities, oxyfuel track torch cutting remains remarkably affordable. Its cost-effectiveness makes it an attractive option for businesses of all sizes, offering high-quality results without breaking the bank.
4. Efficiency: Time is money in the fabrication industry, and oxyfuel track torch cutting doesn't disappoint. Its efficient operation minimizes downtime, allowing businesses to meet deadlines and maximize productivity.
How Does Oxyfuel Track Torch Cutting Work?
Oxyfuel track torch cutting operates on a straightforward yet ingenious principle. Here's a breakdown of its essential components and working mechanism:
1. Torch Assembly: At the heart of oxyfuel track torch cutting is the torch assembly. This comprises the cutting torch, which delivers a stream of oxygen and fuel gas to the workpiece, initiating the cutting process.
2. Track System: Unlike handheld torches, oxyfuel track torch cutting utilizes a track system for precision movement. The track ensures uniformity and consistency in cutting, eliminating errors and enhancing accuracy.
3. Gas Supply: A reliable source of oxygen and fuel gas is crucial for oxyfuel track torch cutting. The gases combine to create a high-temperature flame, capable of melting through various metals with ease.
4. Cutting Table: To support the workpiece during cutting, a sturdy cutting table is employed. This provides stability and ensures precise positioning, enabling flawless execution of cutting operations.
5. CNC Control (Optional): For enhanced automation and programmability, oxyfuel track torch cutting systems may integrate CNC (Computer Numerical Control) technology. This allows for precise control over cutting parameters, resulting in consistent, repeatable cuts.
Conclusion
Oxyfuel track torch cutting isn't just a tool—it's a cornerstone of precision and efficiency in the fabrication industry. Its affordability, versatility, and unrivaled accuracy make it indispensable for businesses striving for excellence. By understanding its usage, affordability, and working principles, fabrication professionals can harness the power of oxyfuel track torch cutting to elevate their craft and achieve remarkable results.
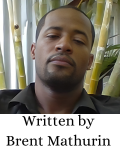
Add comment
Comments