The evolution of metal cutting technology has been marked by significant milestones, with each innovation bringing new capabilities and efficiencies to industrial fabrication processes. Among these advancements, plasma cutting stands out as a groundbreaking method that revolutionized metal fabrication in the latter half of the 20th century. From its humble beginnings in the early experiments with electric arcs to the sophisticated systems of today, plasma cutting has become a cornerstone of modern metalworking.
In this exploration of the history of plasma cutting and its limitations compared to alternative metal cutting methods, we delve into the journey of this transformative technology. While plasma cutting offers numerous advantages in terms of speed, versatility, and precision, it is not without its drawbacks. By understanding the evolution of plasma cutting and its relative strengths and weaknesses, we gain valuable insights into selecting the most appropriate cutting method for various fabrication needs. Let us embark on a journey through time, tracing the arc of plasma cutting innovation and examining its place in the landscape of metal cutting technologies.
Affiliate disclosure: As an Amazon Associate I earn commission from qualifying purchases.
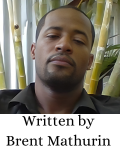
The history of the Plasma Cutter spans over a century, evolving from early experiments with electric arcs to the sophisticated cutting technology we have today.
Here's a brief overview:
Early Electric Arc Experiments (Late 19th Century): The concept of using an electric arc to cut metal dates back to the late 19th century. Engineers and scientists experimented with electric arcs produced by high-voltage currents to melt and cut through metal. However, these early experiments were rudimentary and lacked the precision and control needed for practical industrial applications.
Development of Plasma Cutting (1950s): The modern plasma cutting process began to take shape in the 1950s with the work of researchers like Robert Gage and his team at Union Carbide. They developed the first practical plasma cutting system by introducing a gas flow around an electric arc to create a high-temperature plasma jet capable of cutting through metal. This innovation greatly improved the cutting speed, quality, and versatility compared to traditional methods.
Advancements in Technology (1960s-1980s): Throughout the 1960s and 1970s, plasma cutting technology continued to evolve, driven by improvements in power sources, torch design, and control systems. These advancements led to more efficient and reliable plasma cutting machines suitable for a wide range of industrial applications. By the 1980s, plasma cutting had become a popular method for cutting metal in industries such as manufacturing, construction, and automotive.
Introduction of CNC Plasma Cutting (1980s-1990s): The integration of computer numerical control (CNC) technology with plasma cutting systems in the 1980s revolutionized the industry. CNC plasma cutting allowed for precise, automated cutting of complex shapes and patterns based on digital designs. This made plasma cutting even more versatile and efficient, enabling manufacturers to produce parts with higher accuracy and repeatability.
Continued Innovation and Refinement (2000s-Present): In recent decades, plasma cutting technology has continued to advance with improvements in power efficiency, cutting speed, consumable life, and ease of use. Manufacturers have introduced high-definition plasma systems capable of producing cleaner cuts with narrower kerf widths and reduced dross formation. Additionally, advancements in software integration and automation have further enhanced the capabilities of plasma cutting machines, making them indispensable tools in modern metal fabrication and manufacturing processes.
Today, plasma cutting remains a widely used and versatile method for cutting a variety of metals, including steel, aluminum, and stainless steel, across various industries around the world.
Here are several reasons why a plasma cutters might not always be the best cutting tool for metal fabrication:
Limited Thickness Capability: While plasma cutters are excellent for cutting thin to medium thickness metals, they can struggle with thicker materials. As the thickness increases, the quality of the cut may diminish, resulting in rough edges, dross formation, and slower cutting speeds. For thick materials, alternative methods like oxy-fuel cutting or mechanical sawing may be more suitable.
Cost Considerations: Plasma cutting systems can be relatively expensive to purchase and maintain compared to some other cutting methods. The initial investment includes the cost of the machine itself, as well as ongoing expenses for consumables such as electrodes, nozzles, and gas. Additionally, regular maintenance is necessary to keep the machine in optimal condition, adding to the overall cost of ownership.
Environmental Impact: Plasma cutting generates high temperatures and emits fumes and gases, including ozone and nitrogen oxides, which can be harmful to both the operator and the environment if not properly controlled. Adequate ventilation and safety measures are essential to mitigate these risks. In indoor or enclosed spaces, the environmental impact and safety concerns associated with plasma cutting may outweigh its benefits.
Precision and Accuracy: While plasma cutting is generally faster than other methods like manual grinding or sawing, it may not offer the same level of precision and accuracy, especially for intricate or detailed cuts. Factors such as torch stability, material conductivity, and operator skill can affect the quality of the cut, leading to variations in dimensions and surface finish. For applications requiring tight tolerances, alternative cutting methods such as laser cutting or waterjet cutting may be preferred.
Power Requirements: Plasma cutting requires a significant amount of electrical power to generate the plasma arc and sustain the cutting process. This high power consumption can be a limitation in remote or off-grid locations where access to reliable electricity may be limited or costly. In such cases, alternative cutting methods that are less dependent on electricity, such as oxy-fuel cutting or mechanical shearing, may be more practical options.
Material Warping: Plasma cutting produces heat-affected zones along the cut edges, which can lead to material warping, especially in thin or heat-sensitive metals. This distortion may affect the dimensional accuracy of the cut and require additional machining or straightening operations to correct. For materials prone to warping, alternative cutting methods with lower heat input, such as laser cutting or waterjet cutting, may be preferable.
Noise and Vibration: Plasma cutting can generate significant noise and vibration during operation, which may be disruptive in certain work environments. Operators may need to wear hearing protection, and additional measures may be required to dampen vibrations and minimize noise pollution. In noise-sensitive settings, alternative cutting methods that produce less noise and vibration, such as mechanical shearing or abrasive cutting, may be more suitable.
By considering these factors, fabricators can make informed decisions about the most appropriate cutting method for their specific application requirements.
Add comment
Comments