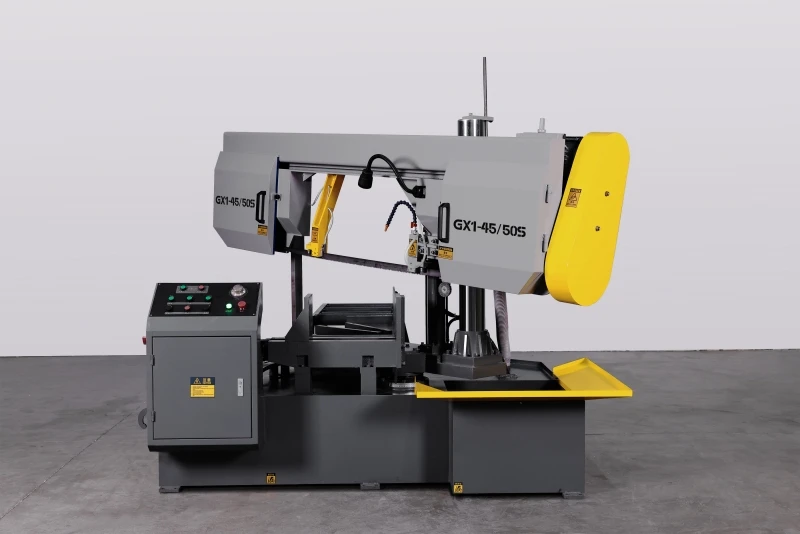
Horizontal Bandsaw
Bandsaws are essential tools in the world of metal fabrication, woodworking, and manufacturing. If you’re considering purchasing a bandsaw or simply want to understand what makes them invaluable, this guide is for you. We’ll cover the history of the bandsaw, how they work, their parts, types, maintenance tips, safety measures, and much more. By the end, you’ll be equipped with all the knowledge you need to make an informed decision about buying and using a bandsaw.
What is a Bandsaw?
A bandsaw is a power tool that uses a continuous loop blade with teeth to cut various materials, including metal, wood, and plastic. Its design allows for smooth, precise cuts, making it a staple in fabrication shops, construction, and manufacturing.
History of the Bandsaw
The first bandsaw patent dates back to 1809, granted to William Newberry in England. However, it wasn’t until 1846 that the bandsaw became practical, thanks to the invention of durable, welded blades by Frenchwoman Anne Paulin Crepin. Over the years, bandsaws evolved into versatile and efficient tools, now used in industries worldwide.
CNC Bandsaw
Parts of a Bandsaw
To understand a bandsaw’s functionality, it’s essential to know its key components:
1. Blade: A loop of metal with teeth, designed for cutting. Blades come in various widths, tooth patterns, and materials depending on the application.
2. Wheel: Bandsaws typically have two wheels (upper and lower) that guide the blade in a continuous loop.
3. Table: The flat surface where the material rests during cutting. It may tilt for angled cuts.
4. Guide System: Blade guides and bearings keep the blade steady for precision cutting.
5. Motor: Provides power to the wheels, determining the cutting speed and efficiency.
6. Frame: The main structure that supports the machine. Frames can be bench-mounted or floor-standing.
7. Tension Adjustment Knob: Ensures the blade is properly tensioned for smooth operation.
8. Fence and Miter Gauge: Accessories to help make straight or angled cuts.
9. Dust Port: For collecting debris, primarily in woodworking bandsaws.
Vertical Bandsaw
Types of Bandsaws for Metal Fabrication
Best for cutting long materials like pipes, bars, and beams.
Offers automatic feeding and stopping features.
Commonly used in industrial settings.
Ideal for intricate and curved cuts.
Often used in tool rooms or smaller fabrication workshops.
Combines manual loading with automated cutting, offering efficiency without the high cost of CNC systems.
4. CNC Bandsaws
Fully automated and highly precise.
Best for high-volume production and repetitive cuts.
Lightweight and mobile, perfect for on-site work.
Semi Automatic Bandsaw
How to Choose the Right Bandsaw
1. Material Type
For metal, look for a high-speed steel blade and a sturdy frame.
For softer materials, a less aggressive blade suffices.
2. Cutting Requirements
Need precise angles? Go for a semi-automatic or CNC bandsaw.
Cutting large volumes? Choose a horizontal bandsaw.
3. Budget
Portable bandsaws: $300–$800.
Semi-automatic bandsaws: $2,000–$50,000.
CNC bandsaws: $5,000–$100,000+.
4. Power Source
Most bandsaws run on 110V or 220V electricity. Industrial models may require three-phase power for higher efficiency.
5. Workload and Space
For smaller workshops, consider a bench-mounted bandsaw.
For high-volume work, invest in a floor-standing or CNC model.
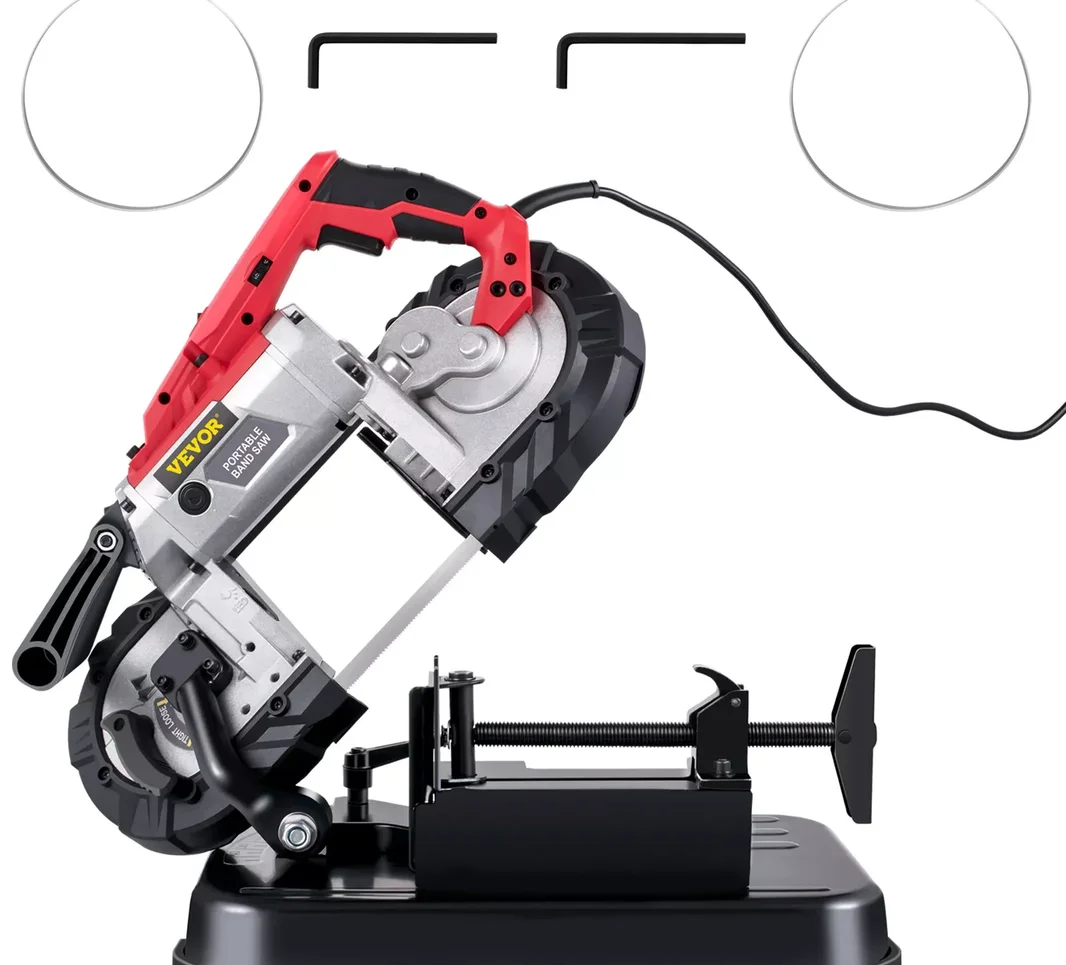
Portable Bandsaw
Efficiency and Functionality
Bandsaws are efficient due to their continuous cutting motion, which minimizes downtime. They are versatile, capable of straight cuts, curves, angles, and even intricate shapes. Semi-automatic and CNC models increase productivity, especially in high-volume environments.
Maintenance and Cleaning
Proper maintenance ensures your bandsaw performs optimally for years:
1. Blade Care
Replace dull or damaged blades immediately.
Clean blades after each use to prevent debris buildup.
2. Lubrication
Lubricate moving parts to reduce wear and tear.
3. Alignment Checks
Regularly inspect blade tension and guide alignment.
4. Cleaning
Remove chips and debris from the machine after every use.
5. Annual Servicing
Schedule professional maintenance annually to check motor performance and overall condition.
Safety and Precautions
1. Use Personal Protective Equipment (PPE)
Wear safety goggles, gloves, and ear protection.
2. Blade Guard
Ensure the blade guard is in place during operation.
3. Proper Feeding
Feed materials steadily without forcing them.
4. Disconnect Power
Always disconnect the bandsaw from power before making adjustments or cleaning.
5. Training
Ensure all operators are trained on proper usage and safety protocols.
How to Purchase a Bandsaw
1. Online Stores
Websites like ours offer a wide range of bandsaws, complete with specifications and pricing.
2. Local Suppliers
Visit local hardware or machinery stores for hands-on comparisons.
3. Used Equipment
For budget-conscious buyers, second-hand bandsaws can be a good option, though thorough inspection is necessary.
4. Financing Options
Many suppliers, including us, offer financing plans to make purchasing easier.
Why Choose Our Bandsaws?
At Industrial Management Systems LLC, we offer high-quality semi-automatic angle bandsaws designed for efficiency and precision. Our machines are competitively priced and built to last, making them the perfect addition to any fabrication shop.
Conclusion
Bandsaws are an indispensable tool for anyone in fabrication, construction, or manufacturing. By understanding their types, parts, and functionality, you can s
elect the right bandsaw to meet your needs. Whether you're looking for efficiency, precision, or versatility, our range of bandsaws will elevate your workshop's performance.
Explore our collection today and take the first step toward optimizing your cutting process!
Customers also checked out:
Add comment
Comments