Affiliate disclosure: As an Amazon Associate I earn commission from qualifying purchases.
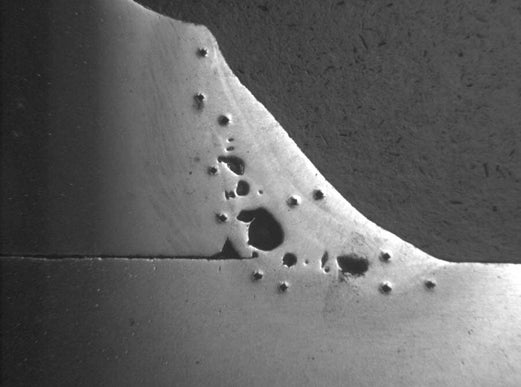
Porosity in aluminum TIG (Tungsten Inert Gas) welding occurs when tiny gas pockets or voids become trapped within the weld. It can weaken the weld and compromise its integrity. Several factors can contribute to porosity in aluminum TIG welding:
-
Contaminants: Aluminum is sensitive to contaminants, particularly moisture and oils. Any surface contaminants on the base metal or filler material can lead to gas pockets in the weld. It's crucial to clean the aluminum thoroughly before welding, using a stainless steel brush or a suitable solvent.
-
Inadequate Shielding Gas: In TIG welding, an inert gas, typically argon, is used to shield the weld area from atmospheric gases. If there is insufficient or inconsistent gas flow, or if the gas nozzle is too far from the weld, it can allow atmospheric gases to mix with the weld pool, leading to porosity.
-
Gas Flow Rate: The flow rate of the shielding gas needs to be properly adjusted to ensure adequate coverage and protection. Too much or too little gas can result in porosity.
-
Dirty or Contaminated Filler Material: The filler rod should be kept clean and free of contaminants. Any impurities on the filler rod can introduce contaminants into the weld.
-
Welding Technique: Inconsistent or improper welding techniques, such as excessive travel speed, too wide an arc, or excessive heat input, can lead to porosity. A stable and controlled welding technique is essential.
- Aluminum Oxide Layer: Aluminum forms a natural oxide layer on its surface, which needs to be removed before welding. Failing to remove this oxide layer through proper cleaning or use of the appropriate techniques (AC welding for aluminum) can lead to porosity.
- Base Metal Thickness: When welding thick aluminum, preheating the material can help reduce the risk of porosity by preventing rapid cooling and gas entrapment.
- Tungsten Contamination: The tungsten electrode used in TIG welding should be free of any contamination. Contaminated tungsten can introduce impurities into the weld pool, causing porosity.
- Gas Diffuser Blockage: The gas diffuser and cup on the TIG torch should be free of obstructions. Blockages can disrupt the flow of shielding gas, leading to porosity.
- Improper Gas Cup Size: Using the correct size of the gas cup for the application is crucial. An incorrect size can affect gas flow and shielding.
- Electrode Angle and Position: Incorrect electrode angle and positioning can result in poor gas coverage and gas turbulence, leading to porosity. Proper electrode angle and positioning are essential for effective shielding.
- To reduce or prevent porosity in aluminum TIG welding, it's vital to pay attention to these factors, maintain cleanliness, use the correct shielding gas, and follow proper welding techniques. Consistent practice and experience can also help improve your welding skills and reduce the risk of porosity.
Add comment
Comments