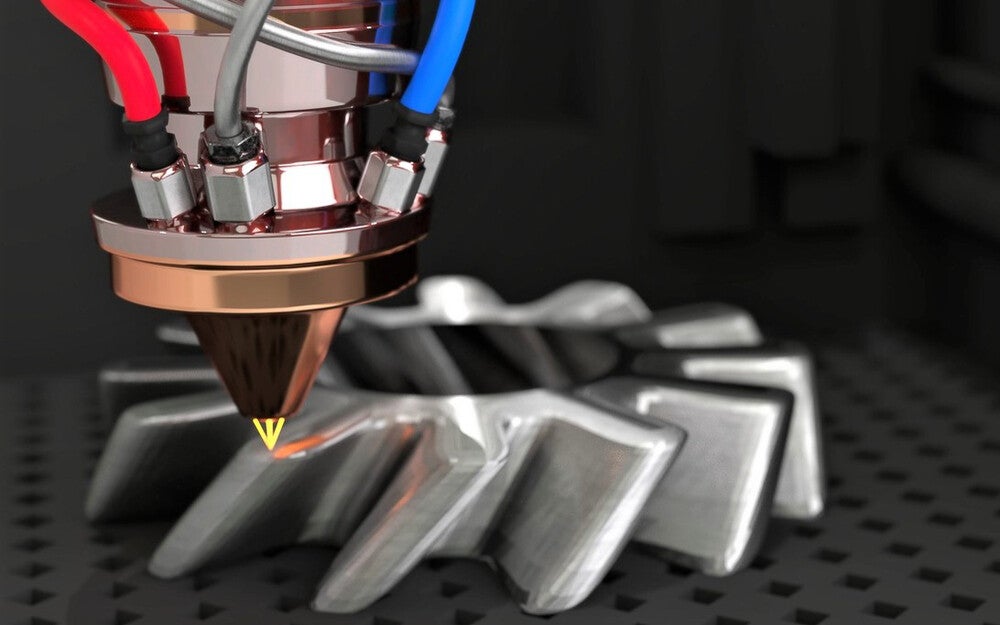
3D metal printing builds up objects layer by layer.
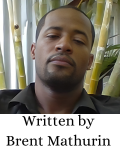
In the realm of modern manufacturing, few technologies have captured the imagination and potential for innovation quite like 3D metal printing. This groundbreaking method, also known as additive manufacturing, offers a paradigm shift in how we conceive, design, and produce metal components. Unlike traditional subtractive manufacturing processes, which involve cutting away material from a solid block, 3D metal printing builds up objects layer by layer, using finely controlled lasers or electron beams to selectively melt metal powders. The result is nothing short of revolutionary: intricate geometries, complex structures, and unparalleled customization possibilities that were once inconceivable are now within reach. As we embark on this journey into the world of 3D metal printing, we'll uncover the fundamental principles, explore the diverse applications, and delve into the exciting frontier of innovation that is reshaping industries and propelling us towards a future limited only by our imagination.
Advantages:
-
Complex Geometries: One of the most significant advantages of 3D metal printing is its ability to create highly intricate and complex geometries that would be difficult or impossible to achieve with traditional manufacturing methods. This opens up new design possibilities and allows engineers and designers to push the boundaries of what is possible.
-
Reduced Material Waste: Unlike subtractive manufacturing processes, which often result in significant material wastage, 3D metal printing is an additive process that only uses the material necessary to build the final component. This not only reduces material waste but also helps minimize costs associated with raw materials.
-
Customization and Personalization: 3D metal printing enables unparalleled customization and personalization, allowing manufacturers to tailor products to meet specific customer needs and preferences. From customized medical implants to personalized aerospace components, this level of customization can lead to improved performance and customer satisfaction.
-
Rapid Prototyping and Iteration: With 3D metal printing, prototypes and small-scale production runs can be produced quickly and cost-effectively, allowing for rapid iteration and design refinement. This accelerated product development cycle can lead to faster time-to-market and a competitive edge in industries where speed and agility are crucial.
-
Weight Reduction and Optimization: Additive manufacturing allows for the creation of lightweight yet structurally optimized components, reducing material usage without sacrificing strength or performance. This is particularly beneficial in industries such as aerospace and automotive, where weight reduction can lead to significant fuel savings and performance improvements.
Challenges:
-
Cost of Equipment and Materials: While the cost of 3D metal printing technology has decreased in recent years, it still remains relatively expensive compared to traditional manufacturing methods. Additionally, the cost of metal powders and other consumables can be significant, especially for high-volume production.
-
Surface Finish and Post-Processing Requirements: Parts produced through 3D metal printing often require post-processing to achieve the desired surface finish and mechanical properties. This can add time and cost to the manufacturing process, particularly for parts with tight tolerances or critical surface requirements.
-
Limited Material Selection: While the range of available metal powders for 3D metal printing is growing, there are still limitations in terms of material selection compared to traditional manufacturing methods. Certain materials may not be suitable for 3D printing due to their properties or processing requirements, limiting the applicability of the technology in certain industries.
-
Quality Control and Certification: Ensuring the quality and consistency of parts produced through 3D metal printing can be challenging, particularly for critical applications such as aerospace and medical devices. Strict quality control measures and certification processes are necessary to validate the integrity and performance of printed components, adding complexity and cost to the manufacturing process.
-
Scale and Production Speed: While 3D metal printing excels in rapid prototyping and small-scale production, it may not be well-suited for high-volume manufacturing due to limitations in production speed and scalability. As a result, traditional manufacturing methods may still be preferred for mass production of certain components.
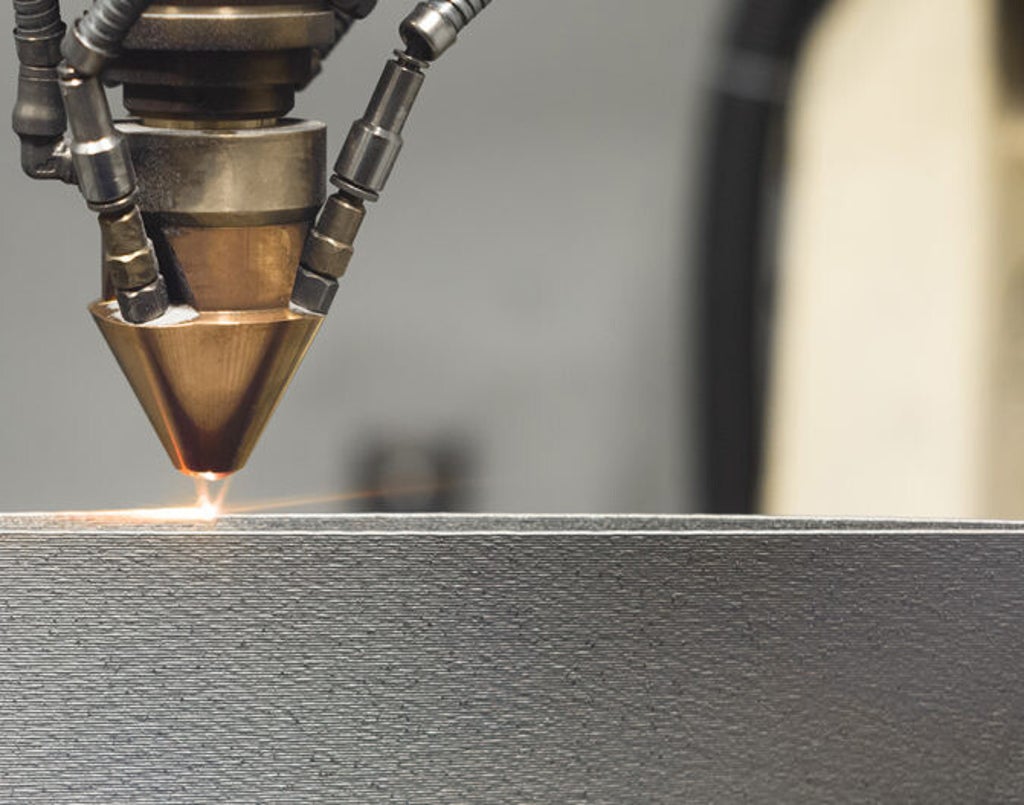
3D metal printing has the potential to complement or even replace traditional welding methods in specific applications, showcasing a synergistic relationship between additive manufacturing and welding. One such application is in the production of complex, customized metal components where traditional welding techniques may be limited by the intricacy of the design. 3D metal printing excels in fabricating intricate geometries layer by layer, offering a level of precision and complexity that traditional welding methods struggle to achieve. By utilizing additive manufacturing, manufacturers can produce highly customized components with minimal material waste and without the need for extensive welding processes. Additionally, 3D metal printing can be used to create integrated assemblies, eliminating the need for multiple welding joints and reducing the risk of weld defects. In industries such as aerospace and automotive, where lightweight, high-strength components are crucial, additive manufacturing can produce parts with optimized geometries and material properties, reducing the reliance on traditional welding methods. Furthermore, 3D metal printing enables rapid prototyping and iteration, allowing engineers to quickly test and refine designs before committing to full-scale production. While traditional welding methods remain indispensable for certain applications, the synergy between additive manufacturing and welding opens up new possibilities for customization, efficiency, and innovation in metal fabrication.
The emergence of 3D metal printing revolutionizes the welding industry, prompting changes in skill requirements and job roles. Welders must now master additive manufacturing techniques alongside traditional skills, necessitating training in CAD software and additive manufacturing processes. New job roles, such as additive manufacturing technicians and materials specialists, arise, requiring expertise in optimizing designs and maintaining 3D printing equipment. This shift also impacts the manufacturing ecosystem, enabling localized production and accelerating product development through rapid prototyping. However, challenges such as material qualification and scalability underscore the need for collaboration and ongoing adaptation to fully harness the potential of 3D metal printing in welding and manufacturing.
Add comment
Comments